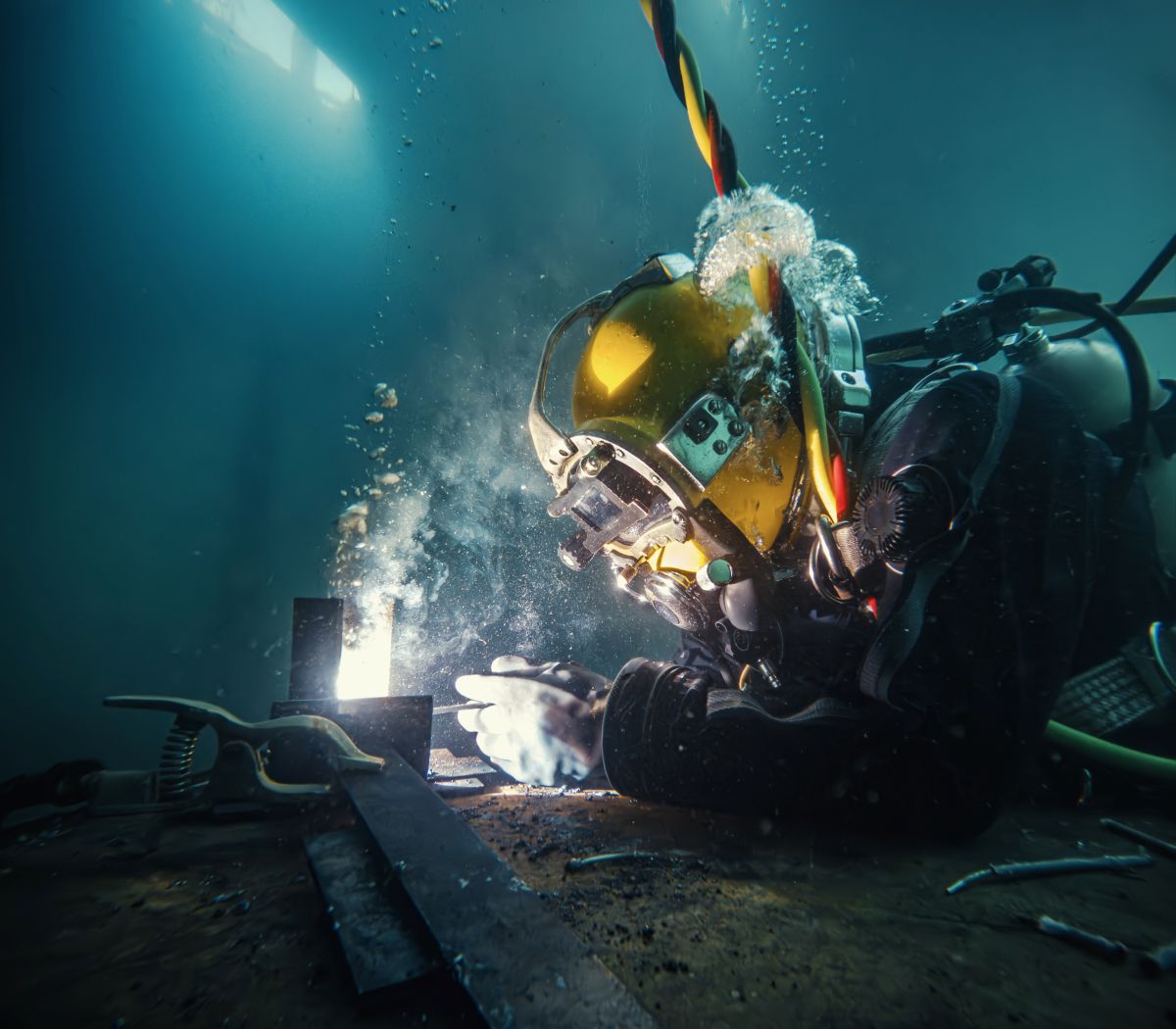
Hyperbaric welding is a fascinating and highly specialized field that merges the precision of welding with the challenges of working in high-pressure underwater environments. This essential technique plays a pivotal role in industries like offshore oil and gas, marine construction, and infrastructure repair, enabling the maintenance and creation of critical structures beneath the surface. From repairing pipelines in the deep sea to ensuring the integrity of submerged infrastructure, hyperbaric welding showcases the blend of advanced technology, skilled craftsmanship, and problem-solving required to tackle extreme conditions.
What is Hyperbaric Welding?
Hyperbaric welding is a specialized welding process performed in high-pressure environments, typically underwater or in sealed chambers filled with pressurized gas. It involves the fusion of metal components under conditions that standard welding methods cannot endure, making it an essential technique for industries like offshore oil and gas, shipbuilding, and underwater infrastructure repair.
Types of Hyperbaric Welding
- Wet Welding: Performed directly in the water, using specialized electrodes that operate under submerged conditions. This method is highly efficient for emergency repairs due to its speed and ease of deployment, but it is prone to challenges like hydrogen embrittlement and reduced weld quality due to water contamination.
- Dry Chamber Welding: Involves creating a small, localized dry zone around the welding area. This is achieved by using a pressurized enclosure to expel water and maintain an air pocket. Dry chamber welding allows for greater precision and improved weld quality, making it suitable for critical structural repairs.
- Habitat Welding: Performed inside a large pressurized chamber that can accommodate welders and equipment. This technique provides an entirely dry environment, regardless of the depth, enabling high-quality, long-duration welding tasks. Although habitat welding is complex and costly, it is essential for large-scale projects where superior weld integrity is non-negotiable.
Historical Background of Hyperbaric Welding
The origins of hyperbaric welding can be traced back to the early 20th century when the need for underwater repairs in shipbuilding and marine engineering first became evident. As naval fleets and offshore industries expanded, traditional welding methods proved inadequate for submerged environments, driving the development of innovative techniques.
The first notable advancements occurred during World War II, as underwater welding became crucial for repairing damaged ships and maintaining naval assets. Early methods relied on rudimentary equipment and carried significant risks, but they laid the foundation for modern hyperbaric welding practices.
By the mid-20th century, the oil and gas industry’s offshore exploration efforts created an even greater demand for reliable underwater welding. Engineers and researchers developed safer and more efficient techniques, including dry chamber and habitat welding, to accommodate deeper and more complex repairs. Advances in materials, pressure management, and welding technology during this period significantly improved the process’s reliability and safety.
Key Techniques
Hyperbaric welding employs a range of specialized techniques to ensure precision and reliability in high-pressure environments. The choice of technique depends on the depth, environmental conditions, and the structural requirements of the project.
Shielded Metal Arc Welding (SMAW):
This is the most commonly used technique in wet hyperbaric welding. It involves the use of waterproof electrodes that create an electric arc between the electrode and the metal surface. The arc generates intense heat, melting the materials to form a strong bond. SMAW is favored for its simplicity and portability, especially in emergency repairs.
Gas Tungsten Arc Welding (GTAW):
GTAW, or TIG (Tungsten Inert Gas) welding, is used in dry hyperbaric environments where precision is paramount. It employs a non-consumable tungsten electrode and an inert gas, like argon, to protect the weld area from contamination. This technique produces high-quality, clean welds, making it ideal for critical structural applications.
Friction Welding:
This innovative method involves the use of mechanical friction to generate heat, allowing materials to fuse without melting. Friction welding is gaining popularity in hyperbaric settings due to its ability to join dissimilar metals and its minimal reliance on consumables.
Flux-Cored Arc Welding (FCAW):
In dry hyperbaric welding, FCAW offers an efficient alternative to traditional methods. It uses a continuously fed electrode wire filled with flux, which creates a protective gas shield around the weld. This technique enhances productivity, especially for large-scale repairs.
Robotic Welding Systems:
As technology advances, robotic welding systems are becoming integral to hyperbaric operations. These systems are remotely operated, ensuring precision and safety in hazardous or inaccessible underwater locations. Robotics also allows for the automation of repetitive tasks, increasing efficiency.
Advantages of Hyperbaric Welding
Hyperbaric welding offers numerous advantages, making it an invaluable process for underwater and high-pressure applications. Its unique ability to provide durable and reliable repairs or fabrications in challenging environments has established it as a critical solution for many industries.
Versatility in Application
Hyperbaric welding is adaptable to a wide range of scenarios, from repairing pipelines and offshore platforms to maintaining ship hulls and underwater structures. Its ability to operate both underwater and within pressurized chambers makes it suitable for diverse projects.
Cost-Effectiveness
By allowing repairs to be carried out on-site without the need to transport damaged components to dry docks or workshops, hyperbaric welding significantly reduces downtime and logistical costs. Wet welding, in particular, is a fast and cost-efficient solution for emergency repairs.
Structural Integrity
The welds created through hyperbaric techniques, especially in controlled dry environments, are known for their high-quality bonds. These welds exhibit excellent durability and strength, ensuring the longevity of the repaired or fabricated structures even under harsh conditions.
Accessibility to Challenging Locations
One of the standout benefits of hyperbaric welding is its ability to function in extreme and remote environments. From deep-sea pipelines to hard-to-reach areas in offshore facilities, this method enables welders to access and repair critical infrastructure that would otherwise remain inaccessible.
Minimal Disruptions to Operations
In many cases, hyperbaric welding allows for repairs to be conducted without fully halting operations. This is especially beneficial in industries like oil and gas, where downtime can result in significant financial losses.
Challenges in Hyperbaric Welding
While hyperbaric welding offers unparalleled benefits for underwater and high-pressure environments, it is not without its challenges. The process requires meticulous planning, specialized expertise, and advanced technology to overcome the inherent difficulties associated with high-pressure and underwater operations.
Safety Risks
Hyperbaric welding poses some risks to welders, including decompression sickness, oxygen toxicity, and nitrogen narcosis. These hazards arise due to the extreme pressures and varying gas mixtures used in the process, necessitating rigorous training and safety protocols.
Equipment Complexity
The equipment required for hyperbaric welding, such as pressurized habitats and waterproof tools, is highly specialized and often expensive. Ensuring proper maintenance and functionality of these tools adds another layer of complexity.
Environmental Challenges
Underwater conditions, such as low visibility, strong currents, and fluctuating temperatures, can make welding operations difficult. These factors demand a high level of skill and adaptability from the welder to maintain precision and safety.
Limited Workforce
The field of hyperbaric welding is highly specialized, and the number of certified professionals is limited. Training welders to operate safely and efficiently in such demanding conditions requires significant time and resources.
People Also Ask
What does a Hyperbaric Welder Do?
- A hyperbaric welder repairs and fabricates underwater structures, working in high-pressure environments using specialized techniques to ensure durability and safety.
How Long Does it Take to Become a Hyperbaric Welder?
- At Commercial Divers International, our program prepares students for a career in underwater welding in under 5 months.
Getting a Career in Hyperbaric Training
At Commercial Divers International, we prepare students for an exciting career in underwater welding with industry-leading training programs. In just four months, you’ll gain the skills, certifications, and confidence needed to work on challenging and high-paying underwater projects. Whether it’s repairing offshore pipelines, maintaining ship hulls, or welding in extreme underwater environments, your future starts here. Take the plunge and start building a career that’s as exciting as it is rewarding.